Increasing efficiency in the warehouse by smart strategies in the ASRS
Smart management of the automated storage and retrieval system (ASRS) starts with initial filling. Goods in the ASRS are mostly stored chaotically. Even for chaotic storage, the WMS (Warehouse Management System) will make sure that one and the same article is stored evenly distributed across all aisles of an ASRS during placement in storage.
There are two reasons for this:
-
If the same item is needed several times at the same moment, spreading it out prevents jams in front of one aisle
-
It also ensures that an item is always available, even if, for example, an aisle is locked due to maintenance
Double cycles for higher efficiency in the warehouse
Many do not know that storage in the ASRS is closely connected to retrieval. The placement strategy is designed so that the aisle/level where the next retrieval is required will be used to keep the performance in an ASRS high. A double cycle is generated in order to avoid empty runs of a robotic carrier and to utilise the facility as well as possible. Efficiency in the ASRS can be preserved while reducing the number of robotic carriers.
Smart warehouse management software and shuttles that are not bound to a level are the key to an efficient warehouse.
ABC categorisation for quick access
In order to ensure the fastest possible access to the items in highest demand, these are stored primarily in the front area of the ASRS. This keeps paths as short as possible.
This requires self-learning systems that conduct a permanent ABC analysis to generate transfer orders, e.g. at night, to transfer A items into the front area of the ASRS and C items into the rear sections. All of these strategies, and, of course, many others, are part of a self-learning material flow computer that is part of a smart Warehouse Management System.
Current trends and information on intralogistics can be found in the new SERVUS Whitepaper:
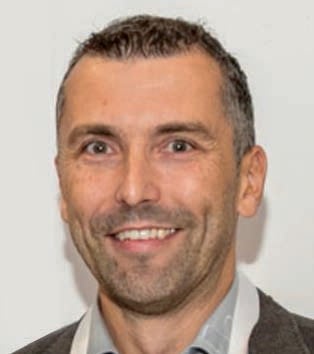
About the author
Managing director at MIA Systems