The ASRS of the Future
Changing consumer behaviour makes products smaller and smaller, more customised and specific for individual customers. Batch sizes in production reduce and product variations increase as a consequence. In order to meet these requirements, production and processes need to adjust and become more efficient. In the best case, production would be just-in-time. This can only work if the warehouse and production are optimally coordinated with each other. The automated storage and retrieval system must be fully integrated into the material flow. This way, the necessary materials can be supplied to production just-in-time after the order is received, inventories in stock can be reduced and available areas can be used for value-added operations.
Introducing Artificial Intelligence
Progress in the area of artificial intelligence will become visible in intralogistics as well. Artificial intelligence will help improve efficiency and storage strategies of intralogistics systems further. For example, algorithms will calculate when which orders should best be processed to smooth out peaks. The warehouse management system will learn when which goods are needed and optimise the warehouse strategy accordingly. Generally, anything that adds value for the customer or increases efficiency will be introduced.
Automatic Picking in the Warehouse
Automatic picking in the ASRS is one of these measures. In a combination of robotic carrier and articulated arm robot expands use of an ASRS and essentially contributes to increasing output. Automated picking in the ASRS merges two processes into one. The system can work independently at night and on weekends as well to essentially contribute to smoothing out peaks. Full automation of the picking process would additionally considerably increase efficiency. The picking robots would be able to prepare the materials before the production shift starts. Picking could be performed in three shifts. The continuous flow has many positive effects throughout the chain. Set formation is another way of using these “automated picking” systems. For the automotive example, this could mean that matching sets comprising equipment, material and/or colour versions are compiled just before assembly. i.e. in the actual sequence and staged for the lines.
The question that keeps coming up is: how can I integrate the “upstream” process into intralogistics as well?
Throughput Times Grow Even Shorter
Further potential can be found in picking orders arriving at the picking robot within seconds after the order is received. Picking can commence immediately then. The throughput times in production could be shortened considerably by this.
Automated Goods Receipt – Expanded Integration of the Supply Chain
In the scope of increasing digitalisation and implementation of industry 4.0 subjects, the upstream supply chain moves more and more into the focus of automation. Suppliers are involved, mapping into the systems is expanded step by step. The question that keeps coming up is: how can I integrate the “upstream” process into intralogistics as well? Recurring deliveries are to be integrated. This means that the supplier delivers its products in matching boxes with unique IDs. Goods receipt only is to take care of booking and handover to the intralogistics system. Master details and any inspection notes are taken over and items are fully automatically integrated into the storage system. The required processes are triggered. Repacking and labelling are no longer necessary. The supplier stores directly into the fully automated and digitised logistics system. Storage and retrievals are noted directly in the warehouse management system. Goods received are available in real time. Subsequently, stocks in circulation continue to reduce and the ASRS is integrated directly into the material flow. Parcels shipments can be stored directly under certain prerequisites as well. If the rules permit, the packages can be stored in the system by tray, and after marrying the package to the try by the deliverer. This is even possible outside of the operating hours if the system is built right.
These scenarios have long ceased to be visions of the future. They will be introduced into company’s warehouses soon.
Current trends and information on intralogistics can be found in the new SERVUS Whitepaper:
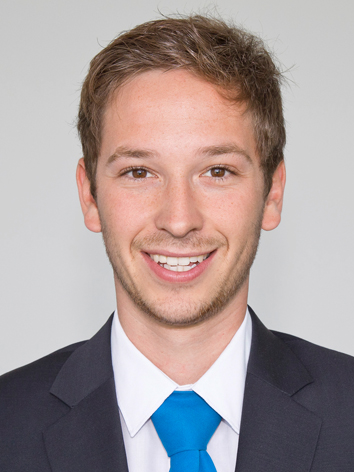
About the author
Dominik Kirchmann is Product Manager at Servus Intralogistics