There were times when the two areas of warehouse and production were strictly separated like two kingdoms. Both worked side by side. Instead of the pull principle, the push principle was practised, warehouses were seen as isolated solutions. Although this is still often the case, it is no longer keeping with the times. Nowadays, an automated storage and retrieval system (ASRS) should be fully integrated into the flow processes and serve as a production buffer. The ASRS should supply production areas directly and at the right time with the right material. This brings several advantages - and thus future security. As a result, the company remains competitive in the age of Industry 4.0:
- Faster processing times in production
- Circulating stocks are reduced
- Production downtime and waiting times are a thing of the past
- Fewer interfaces
- Search times are eliminated
- Process quality is increased and errors are reduced
- All data is available in real time
This ensures that warehouse and production are perfectly synchronized and that the warehouse can be kept as small as possible but as large as necessary - "after all, the best warehouse is one you don't have".
However, the prerequisite for this is that the work carried out in the ASRS is highly efficient and without downtime. Maximum process reliability must be guaranteed. There must be no failure of individual rows or levels or even a total failure of the system.
For the warehouse to be fully integrated into the flow process, unnecessary interfaces should be eliminated and, if possible, production should be supplied with the same transport system.
High speed in the replenishment
What an automated storage system that is fully integrated into the flow processes means for the customer is shown by the example of our client Phonak. The specialist for high-quality hearing aids uses the Servus system at its production site in Stäfa near Zurich along the entire value chain. The Servus transport robots collect the goods at incoming goods, bring them to the warehouse, to order picking, and to the right place to the production area just-in-time. At Phonak, the automated storage system is fully integrated into the flow process, ensuring the fastest possible access times. The absence of interfaces and the associated continuity of data transfers mean an enormous increase in processing times for Phonak: when a hearing aid is sold in a shop in New York and is scanned at the checkout, it automatically triggers a new production order for this type of hearing aid in Stäfa and our transport robots set off - without manual ordering, without an additional work step, fully automated.
"Only when the automated storage system is customised to the customer's needs, can it be integrated into the flow process and become a so-called breathing buffer."
The warehouse as a breathing buffer
Have you ever heard of the warehouse as a "breathing buffer"? In times of batch size 1 and same-day delivery, items no longer lie in the warehouse for weeks. Every customer has an individual need. When planning, it is important to ask yourself questions about the nature of the goods in advance: Is it a fast or slow-moving warehouse? What are the required cycle times? Should supermarkets be integrated? How much space is available? Where is the warehouse best placed? How many items are to be stored? Solutions have to be found here - and these are usually individual. Therefore, time should be taken and everything should be carefully thought through.
Only when an automated storage system is customised to the customer's needs, can it be integrated into the flow process and become a breathing buffer. When logistics and production merge into one unit, the way is paved for lean logistics and the networked factory of tomorrow.
The picking strategy and technology should also always be customised. With pick-by-scan, pick-by-light, pick-by-vision, and much more, there are almost innumerable possibilities. This requires an intensive discussion with the customer in order to subsequently address the customer's wishes in a targeted manner and then develop or implement the appropriate picking solution.
Furthermore, the question arises as to whether centralised picking stations should be realised in connection with a central warehouse or decentralised picking units with associated buffer stores, i.e. picking is carried out where the material is needed.
A decisive factor for future security is flexibility. Despite all automation, the capacity of an ASRS has to be easily expandable and its performance has to be be scalable. This is the only way a company can remain effective in the future and react dynamically to market developments.
When introducing a new automated storage system, many questions need to be answered. An intensive examination of the material flow is inevitable in order to work out the best solution together with the customer. A customised system can be adapted to individual needs – your needs.
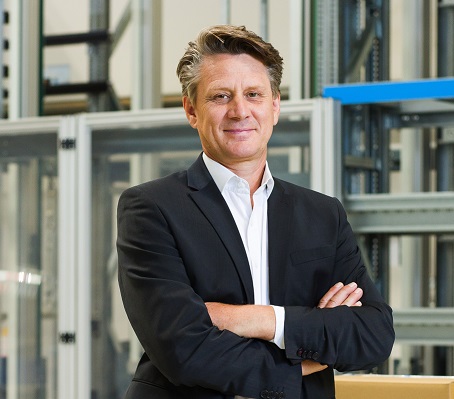
About the author
Christian Beer is the owner and managing director of the Heron Group with the companies Heron CNC-Technik, Robotunits, Servus Intralogistics and SAFEDI.